Exploring Wheel Loader Pallet Forks: Functionality and Benefits
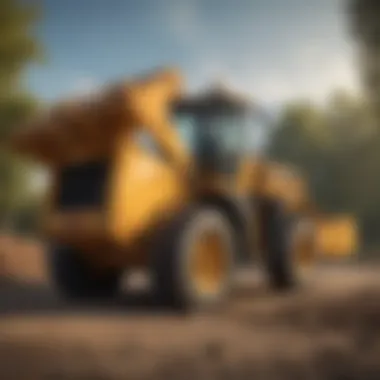
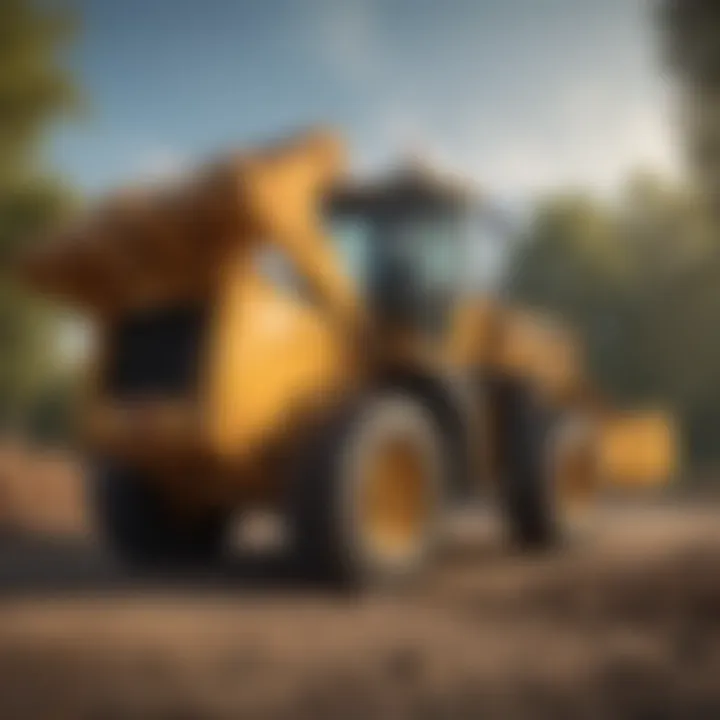
Intro
Wheel loader pallet forks are crucial attachments for enhancing the versatility of wheel loaders in various sectors, particularly in agriculture and industry. Understanding how these tools function, their applications, and the advantages they bring is essential for both professionals and enthusiasts. This exploration not only covers the basic functionalities but also delves into design considerations, operational tips, and maintenance practices. The growing importance of efficient material handling signifies why knowledge in this area is beneficial.
Key Insights
Overview of the Topic
Pallet forks attached to wheel loaders facilitate the efficient handling of materials, particularly pallets in agriculture and industrial environment. They are designed to provide a stable, strong connection to the loader, allowing users to lift and transport heavy loads. These forks maximize productivity by improving load handling capabilities. Their adaptability means they can support various tasks, from moving bales of hay on farms to transporting crates in warehouses.
Importance in Agriculture/Horticulture/Agronomy
In agricultural contexts, pallet forks are instrumental in tasks such as loading and unloading goods, transporting feed, and managing raw materials. The ability to handle heavy pallets reduces manual labor and increases efficiency. Farmers benefit from integrating these tools into their machinery because they streamline operations. In horticulture and agronomy, where precision is key, pallet forks allow for careful management of products without damage.
Sustainable Practices
Eco-Friendly Techniques
Adopting sustainable practices with wheel loader pallet forks contributes to environmental stewardship. For instance, choosing equipment with durable materials reduces waste due to less frequent replacements. Also, regular maintenance ensures optimal performance, minimizing unnecessary fuel consumption.
Case Studies on Sustainability
Many agricultural operations have successfully integrated pallet forks into their sustainability efforts. For example, a case study on farm management highlighted a decrease in soil compaction and fuel usage by utilizing pallet forks instead of traditional lifting methods. This transition not only proved beneficial for the environment but also enhanced overall productivity.
Tools & Resources
Essential Equipment and Technologies
To use pallet forks effectively, several essential tools are needed:
- Wheel Loader: A versatile machine that powers various attachments, including forks.
- Pallet Forks: Different sizes and designs cater to unique lifting needs.
- Safety Gear: Including gloves and helmets to ensure operator safety during operations.
Recommended Books and Readings
For those looking to deepen their understanding, several resources are valuable:
- "The Mechanics of Lift" by Kenneth Brooks
- "Material Handling Equipment" by Luke Adams
- Articles on platforms like Wikipedia and Britannica.
"Well-maintained equipment lasts longer and operates more efficiently; this is especially true for material handling machinery."
This exploration aims to present wheel loader pallet forks as not only practical tools but also integral components in modern agricultural practices. By understanding their functionality and maintenance, users can maximize their investment and efficiency.
Foreword to Wheel Loader Pallet Forks
Wheel loader pallet forks are crucial attachments that enhance the versatility of wheel loaders. They enable operators to lift and transport a variety of materials with greater efficiency. This section discusses the importance of understanding these tools, focusing on their functionality and relevance in agricultural and industrial settings.
Definition and Purpose
Wheel loader pallet forks are a type of fork attachment used on wheel loaders. Their primary purpose is to enable the lifting and transportation of pallets and other heavy loads. These forks attach easily to the loader's arms, transforming it from a bucket loader into a versatile material handling machine. The design allows for significant weight capacities, accommodating various tasks across numerous industries.
Industry Applications
Wheel loader pallet forks find applications in several industries, each benefiting from their unique characteristics.
Agriculture
In the agricultural sector, these pallet forks are used for moving large quantities of feed, fertilizer, and other supplies. The key characteristic of agriculture is its reliance on efficient labor and machinery. Using pallet forks increases productivity on farms by minimizing the time spent transporting materials. One unique feature is their ability to handle bulk items, which is very beneficial during peak seasons.
Construction
Construction sites also leverage wheel loader pallet forks. They are essential for moving materials like lumber and bricks. The construction industry demands robust solutions that can handle heavy loads with precision. Wheel loader pallet forks fulfill this requirement, allowing for efficient loading and unloading. However, their effectiveness is limited by site accessibility, which can be a challenge.
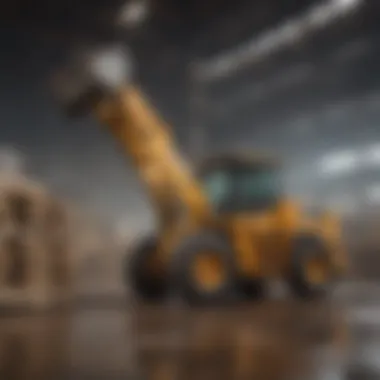
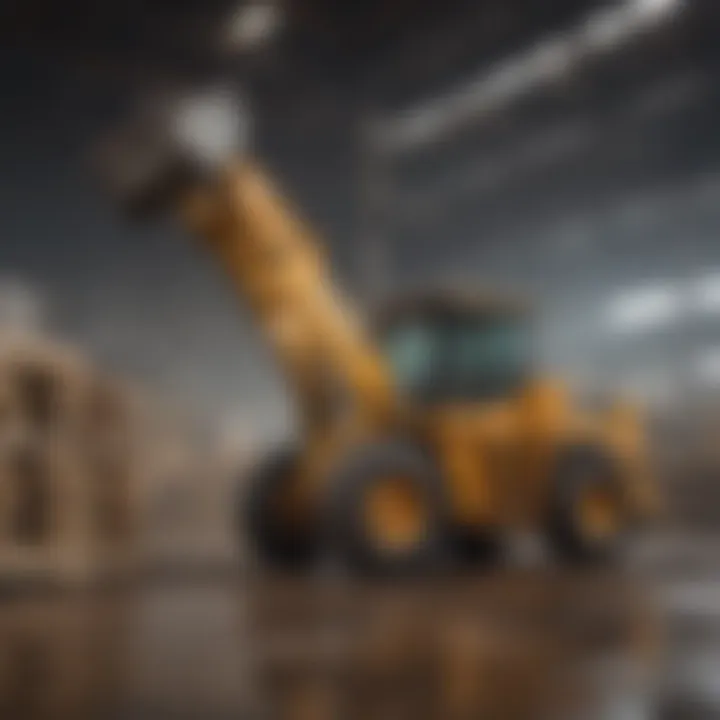
Warehousing
In warehousing, pallet forks are instrumental in facilitating the quick relocation of products. Warehouses require systems that support high turnover rates. The ability of wheel loader pallet forks to handle larger pallets adds to their appeal in this context. However, the need for trained operators is crucial to prevent accidents, which can be a downside.
"Understanding the applications of wheel loader pallet forks allows professionals to optimize their usage and improve overall efficiency."
In summary, the versatility and efficiency of wheel loader pallet forks make them valuable in agriculture, construction, and warehousing. Understanding their purpose and applications can greatly enhance material handling processes across these industries.
Types of Wheel Loader Pallet Forks
Understanding the various types of wheel loader pallet forks is essential for effective material handling. Different designs offer distinct advantages depending on the specific tasks and environments in which they are used.
Standard Pallet Forks
Standard pallet forks are the most common type for wheel loaders. They are designed for general material handling tasks, making them suitable for a wide range of applications. These forks usually come in fixed lengths and widths, ensuring a good balance between stability and maneuverability. Their simplicity makes them easy to attach and detach. Farmers and warehouse operators appreciate them for their reliability and efficiency. They work well with standard-sized pallets and are often used for transporting bulk materials and equipment.
Heavy-Duty Forks
Heavy-duty forks are engineered for more rigorous tasks. They are thicker and stronger, constructed using high-grade materials. These forks can handle larger loads, making them ideal for construction sites or industrial applications. Users appreciate their enhanced durability, which translates into a longer lifespan and less maintenance to consider. It is important in manufacturing and construction where productivity is key. Operators should always consider the specific weight limits of these forks to ensure safe handling.
Adjustable Forks
Adjustable forks offer flexibility that standard and heavy-duty options do not. They feature sliding mechanisms that allow operators to modify the spacing between the fork blades. This adjustability helps in handling various pallet sizes and load types, making them a favorite for diverse handling projects. They are especially useful in environments with varying material dimensions or when operators need to switch between different types of goods frequently.
Custom-Fabricated Options
Custom-fabricated pallet forks are tailored solutions designed to meet specific requirements. If conventional options do not fit the job, these forks can be customized in length, width, or weight capacity. Manufacturers can incorporate unique features based on the operator’s needs, such as additional reinforcement or specific mounting styles. This adaptability can greatly improve efficiency in unique handling situations. However, it is important to work with experienced suppliers to ensure quality and safety.
In summary, selecting the correct type of wheel loader pallet fork is crucial for enhancing operational efficiency and safety. Each type serves specific methods and requirements, highlighting the importance of understanding their distinct features. This knowledge ensures that operators can choose the right tools for their agricultural or industrial projects.
Key Features of Pallet Forks
The design and functionality of wheel loader pallet forks are critical for their effectiveness in material handling. Understanding the key features is essential for anyone who operates or relies on these tools in agriculture or industrial settings. Each feature has a specific role that contributes to the overall performance and safety of the operations.
Material Construction
The material construction of pallet forks directly impacts their durability and performance. Commonly, they are made from high-strength steel alloys. This material can withstand heavy loads and resist bending or deformation. Different forks may use varying grades of steel, where an increased thickness can contribute to overall strength.
In some instances, manufacturers may apply additional coatings to prevent corrosion. This is especially important in environments where moisture, chemicals, or varying temperatures are present. Proper material selection ensures that the forks can endure operational demands without significant wear.
Weight Capacity Considerations
When selecting pallet forks, considering the weight capacity is crucial. Each model has a designated weight limit that should not be exceeded. The capacity often depends on the design and materials used, as well as the type of wheel loader it is paired with. Typically, standard forklift forks can handle loads from 3,000 to 10,000 pounds or more.
It is vital to evaluate the load requirements carefully. Overloading can lead to tipping hazards or equipment failure, which can be dangerous. Regular audits of weight limits and adjustments based on operational demands can help in maintaining a safe working environment.
Fork Blade Design
The fork blade design significantly influences the efficiency of the handling tasks. Pallet forks can come in various widths and length options. The length of the blades affects their ability to stabilize the load; longer forks can handle bigger pallets but may reduce maneuverability.
Additionally, the shape of the fork blades can vary, impacting how the load is secured. For instance, tapered blades are designed to slide easily under pallets, which minimizes risk of damage. Users should always select the design that aligns with the types of loads that will be handled most frequently.
The right combination of material, weight capacity, and design is essential for optimal performance and safety.
These features collectively enhance the productivity of wheel loader pallet forks by ensuring they can perform effectively across various industrial and agricultural tasks.
Benefits of Using Wheel Loader Pallet Forks
Wheel loader pallet forks are essential tools in the material handling industry, especially within agriculture and industrial settings. Understanding the benefits of using these forks can help operators optimize their operations, reduce costs, and increase productivity. The significance of these benefits can not be overstated for farmers and businesses looking to improve their productivity.
Increased Efficiency
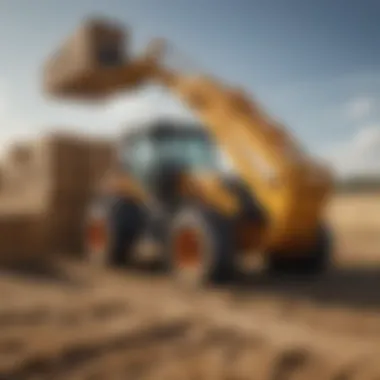
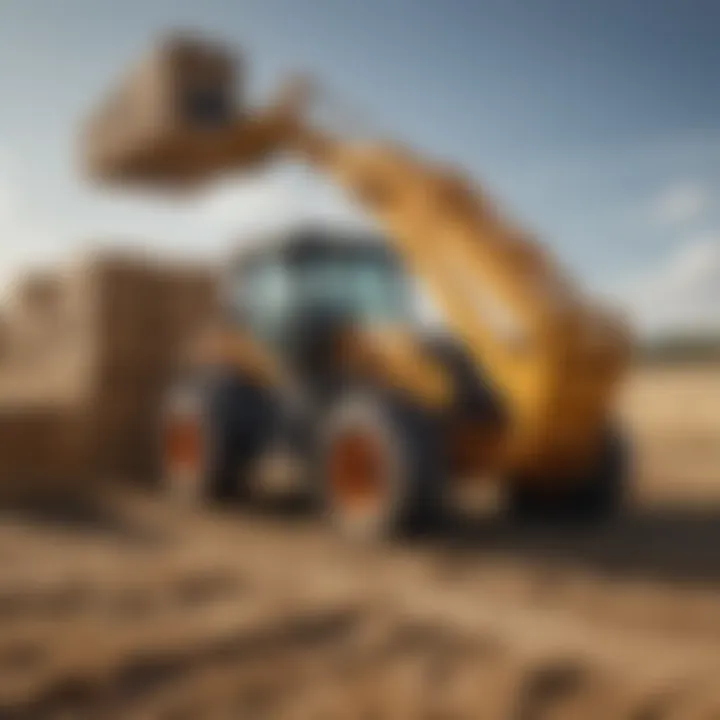
One of the primary advantages of wheel loader pallet forks is the marked increase in efficiency they offer. These forks allow operators to swiftly pick up and move large stacks of materials, such as pallets filled with grain or equipment. When compared with traditional manual handling, the speed at which wheel loader pallet forks operate can dramatically decrease the time required for tasks like loading and unloading. This increase in operational speed translates directly to quicker turnaround times, which is vital in industries where timing is crucial.
Using wheels loader pallet forks also reduces the physical strain on workers. They operate with minimal exertion while effectively lifting heavy loads. In agriculture, for instance, timely handling of harvest products is crucial. Wheel loader pallet forks facilitate efficient transport from field to storage or distribution sites, ensuring a seamless workflow.
Versatility in Handling
Wheel loader pallet forks are not only about efficiency; versatility is another significant benefit. These forks can handle a range of materials, making them useful across various sectors. In agriculture, they can lift bales of hay, pallets of fertilizer, or bags of feed. In construction and warehousing, they can manage heavy equipment and materials like lumber or concrete blocks.
The adjustability of many pallet forks enhances their versatility. Operators can adjust the fork width to accommodate different pallet sizes or cargo types. This flexibility ensures that one piece of equipment can serve multiple purposes, making it a practical investment for any operation.
In addition, these forks can often be used with different attachments, extending their functionality even further. For instance, some wheel loader models allow for the use of hydraulic attachments that enhance the loading capabilities, thus broadening the range of tasks that can be accomplished.
Reduced Labor Costs
Another compelling benefit of wheel loader pallet forks is the reduction in labor costs associated with their use. With the efficiency and versatility mentioned earlier, fewer workers are necessary to complete tasks that once required larger teams. Operators equipped with these forks can achieve the same outcomes more quickly, allowing businesses to allocate their workforce more strategically.
The financial implications are profound. By streamlining operations and decreasing the need for manual labor, businesses reduce their overall labor expenses while maintaining productivity levels.
Furthermore, less physical labor reduces the risk of injuries among workers, leading to lower injury-related costs and insurance claims. This aspect is particularly relevant in agricultural settings where repetitive motions can lead to fatigue and injuries. Investing in wheel loader pallet forks thus not only improves operational efficiency but also contributes to a safer and more sustainable working environment.
"Investing in wheel loader pallet forks is an investment in improved productivity, worker safety, and overall operational success."
In summary, the benefits of using wheel loader pallet forks are substantial. Increased efficiency streamlines operations, versatility in handling expands their applications, and reduced labor costs provide economic advantages. For farmers and industry professionals, integrating these tools into their processes can lead to significant operational improvements.
Operational Best Practices
Operational best practices are essential for ensuring the effectiveness and safety of wheel loader pallet forks in various settings. These practices not only enhance the efficiency of operations but also play a significant role in preventing accidents and prolonging equipment life. By following established techniques, operators can maximize the performance of pallet forks while minimizing risks associated with material handling.
Proper Loading Techniques
Proper loading techniques are crucial to maintain stability and prevent accidents during operation. When using pallet forks, it is important to center the load properly on the forks. Uneven weight distribution can lead to tipping or a loss of control. Operators should ensure that the load is stable before lifting. For heavier items, it is advisable to lift from a lower position to reduce the center of gravity. Furthermore, securing the load with straps or chains can provide additional safety during transport.
Safe Maneuvering Procedures
Maneuvering with loaded pallet forks requires heightened awareness and caution. Operators should always maintain a clear line of sight and drive slowly, especially in crowded or tight spaces. It is important to avoid quick turns and sudden stops, as these actions can destabilize the load. Using spotters in complex situations can enhance safety. Operators should also be aware of their surroundings, including overhead hazards and uneven ground, to reduce the chances of accidents.
Regular Training for Operators
Regular training for operators is vital to ensure that they remain knowledgeable about best practices and equipment functionality. Training sessions should cover topics like load management, handling techniques, and emergency procedures. Operators need to stay updated on the latest safety standards and technological advancements in pallet fork design. Consistent training not only improves safety but also increases overall productivity by fostering confidence in operators to handle equipment effectively.
"Investing time in proper training and safe operational techniques significantly reduces the risk of accidents and ensures long-term efficiency."
Maintenance and Care
Maintaining wheel loader pallet forks is crucial to ensuring their longevity and performance. Regular upkeep helps prevent breakdowns and ensures safe operations. This section discusses key maintenance practices, covering elements central to routine inspections, lubrication, weather protection, and fork replacement guidelines.
Routine Inspections
Routine inspections are vital for identifying wear and tear on wheel loader pallet forks. Regular checks allow operators to spot issues before they escalate into more significant problems. Scheduled inspections should include checking the fork frame for cracks, checking the hydraulic systems for leaks, and ensuring all pins and bushings are secure.
- Inspect for visible damage or deformation.
- Evaluate the condition of hydraulic hoses.
- Check the attachment points for wear.
- Confirm the proper alignment of the forks.
It is also wise to review the manufacturer’s recommendations regarding inspection intervals. Following these guidelines ensures that forks operate efficiently and safely.
Lubrication and Weather Protection
Lubrication is essential for the smooth operation of wheel loader pallet forks. Proper lubrication reduces friction between components, which can lead to faster wear. Focus on applying lubricant to moving parts such as pivot points and joints. Utilizing the right type of lubricant based on the manufacturer’s specifications can extend the life of the forks.
Weather protection is also significant. If pallet forks are exposed to outdoor conditions, protective measures are necessary. Consider the following techniques:
- Use a protective tarp or cover during inclement weather.
- Store forks in a sheltered location when not in use.
- Apply rust-resistant coatings to exposed metal parts.
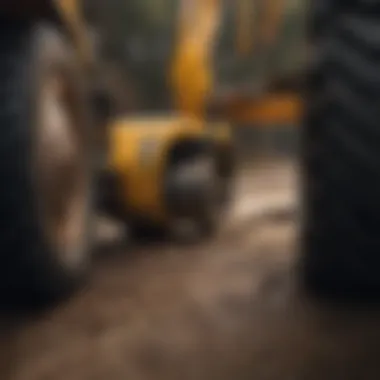
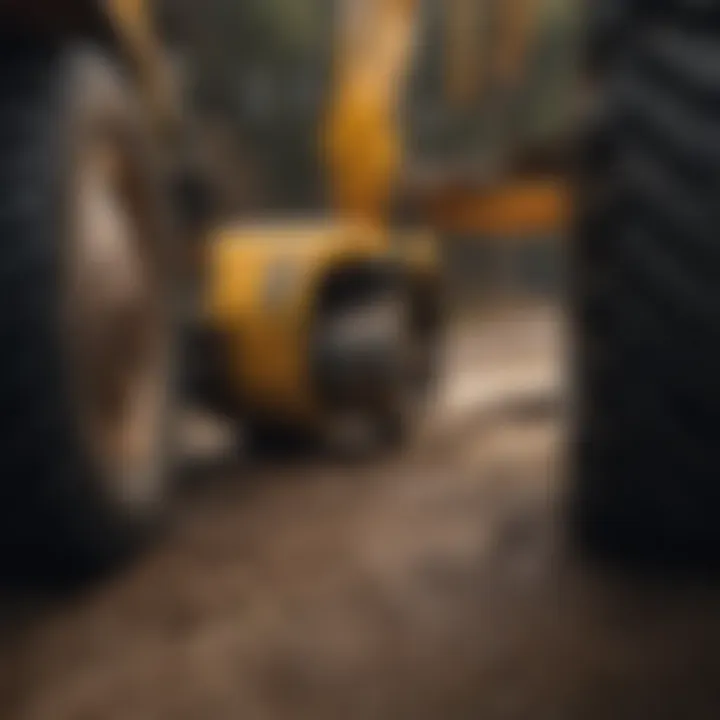
These practices help maintain functionality and aesthetics, preventing corrosion and damage over time.
Fork Replacement Guidelines
Understanding when to replace fork elements is critical. Replacement needs may arise due to bending, cracking, or other forms of degradation. Operators should establish clear guidelines for replacement based on observed wear and the manufacturer's recommendations.
Key indicators for replacement include:
- Forks that show signs of excessive bending or deformation.
- Cracks visible on the surface that could compromise strength.
- Significant wear on forks that fail to meet operational standards.
Following these guidelines helps ensure safety and efficiency in operations. Always involve trained personnel in the assessment and replacement process to maintain safety standards.
Regular maintenance not only prolongs the lifespan of wheel loader pallet forks but also significantly enhances operational safety and efficiency.
Economic Considerations
Economic considerations are vital when evaluating the use of wheel loader pallet forks. These tools can significantly affect the bottom line of operations in agriculture and industry. Properly understanding these fiscal aspects ensures that businesses can make informed decisions regarding their equipment investments. The analysis begins with the initial capital outlay and the potential returns derived from using these attachments.
Initial Investment vs. Cost Savings
Purchasing wheel loader pallet forks represents a substantial initial investment. The upfront costs can vary widely based on the type and brand of forks chosen. Standard pallet forks may be more affordable but might not offer the durability of heavy-duty versions. Thus, the decision typically involves analyzing both the price and the utility of the chosen products.
Once in operation, however, operators often find that the cost savings generated by pallet forks outweigh their initial purchase costs. Using wheel loader pallet forks improves speed and efficiency in material handling, thereby reducing the time spent on moving items. For instance, in a warehouse context, quick loading and unloading translate to faster operational cycles. Additionally, reducing manual labor correlates directly with decreased labor costs, which is beneficial for any business.
The advancement in technology has also led to enhanced designs that require less maintenance and have longer lifespans. Over time, well-maintained pallet forks can lead to significant savings by minimizing repair costs. In summary, while the initial investment is notable, the potential for cost savings, when employed effectively, can make the ownership of wheel loader pallet forks economically favorable.
Factors Affecting ROI
Understanding the return on investment (ROI) for wheel loader pallet forks involves examining various factors. These factors can heavily influence the overall financial success of employing such equipment.
- Utilization Rate: The frequency of use directly affects the ROI. Forks that are used regularly in operations provide better returns compared to those that sit idle.
- Cost of Alternatives: The expense associated with manual labor, or less efficient machinery, needs to be considered. If pallet forks can replace these higher costs, ROI improves.
- Maintenance Practices: Regular maintenance can enhance the longevity and performance of the forks, thereby contributing to better ROI. Poorly maintained equipment may lead to greater downtime and increased repair costs.
- Market Prices: The economic climate and demand for goods can influence how efficiently operations run. High demand periods can lead to quicker turnover rates, further boosting ROI.
- Customization and Adaptation: Custom-fabricated forks that cater to specific operational needs can also enhance efficiency, making the overall investment more worthwhile.
Safety Standards and Regulations
The operation of wheel loader pallet forks falls under various safety standards and regulations. These guidelines are vital as they ensure the safe handling of materials and protection for both operators and bystanders. Compliance with these recommendations not only mitigates risks but supports the sustainablity of operations in agriculture and industry contexts.
National Guidelines
National guidelines govern the safe operation of machinery, including wheel loaders equipped with pallet forks. These regulations often originate from federal agencies such as the Occupational Safety and Health Administration (OSHA) in the United States. OSHA outlines requirements for operator training and safety gear, emphasizing the importance of proper procedures to prevent accidents.
In addition to OSHA, each state may have its own specific regulations that supplement national standards. Companies must stay informed about both to ensure comprehensive compliance. Failure to adhere to these guidelines can lead to severe penalties or accidents that may disrupt workflows.
Manufacturer Safety Recommendations
Beyond governmental regulations, manufacturers of wheel loader pallet forks provide their own safety recommendations. These guidelines typically cover operational limits, recommended maintenance schedules, and the proper use of protective equipment. Adhering to manufacturer instructions can significantly reduce wear and damage, prolonging the service life of the equipment.
Proper operator training is another area highlighted by manufacturers. They often offer training programs or resources to educate operators regarding effective handling techniques and safety practices. Regular training and refreshers help maintain awareness of potential hazards.
It is essential to integrate both national guidelines and manufacturer recommendations in daily operations. Doing so not only enhances safety but also optimizes productivity in material handling processes.
Future Trends in Wheel Loader Pallet Forks
The evolution of wheel loader pallet forks is critical for several industries that depend on effective material handling solutions. As technology progresses, user needs shift, and sustainability becomes a priority, understanding the future trends in this area can provide valuable insights for professionals in agriculture and construction sectors. Businesses that remain informed about these developments can enhance efficiency, reduce environmental impact, and foster operational improvements.
Advancements in Technology
Technological innovations are significantly shaping the design and functionality of wheel loader pallet forks. Key trends include the integration of smart technologies and automation into pallet fork systems, which can enhance precision and safety. For example, digital monitoring systems can provide real-time data about load weight and stability. Leveraging this data may help prevent overloading and maintain safe operating conditions.
Moreover, manufacturers are developing forks with advanced materials that improve durability, reduce weight, and increase lifting capacity. Features like quick-attach systems are also becoming standard, allowing operators to change attachments swiftly without downtime. These advancements contribute to not only improved performance but also to operator safety and comfort.
"Using smart technology in wheel loader pallet forks can lead to safer and more efficient operations in heavy industries."
Sustainability Initiatives
Sustainability is gaining momentum and is a top priority for many sectors. The trend towards eco-friendly designs is evident in the development of wheel loader pallet forks. Manufacturers are focusing on using recyclable materials and methods that reduce energy consumption during production. This shift is important as it meets the growing demand for responsible manufacturing processes that align with global sustainability goals.
Furthermore, the implementation of electric and hybrid models in machinery signifies a shift towards reducing carbon footprints. These machines can be used with pallet forks without compromising power. As businesses increasingly adopt sustainable practices, having environmentally friendly equipment will not only comply with regulations but also appeal to a more eco-conscious market.
In summary, the future of wheel loader pallet forks is powered by technological advancements and sustainability. Keeping pace with these changes is essential for enhancing productivity while supporting a cleaner environment, ultimately benefiting all stakeholders involved.